The scaffold coupler was developed by StrucTemp and LUMA-ID and showcased at the Futurebuild trade fair in January.
For two years a prototype has been handled with great care, whether in the hands of the product design company that produced it or the civil engineer whose experience in the construction industry spawned the idea for it. Steel Board
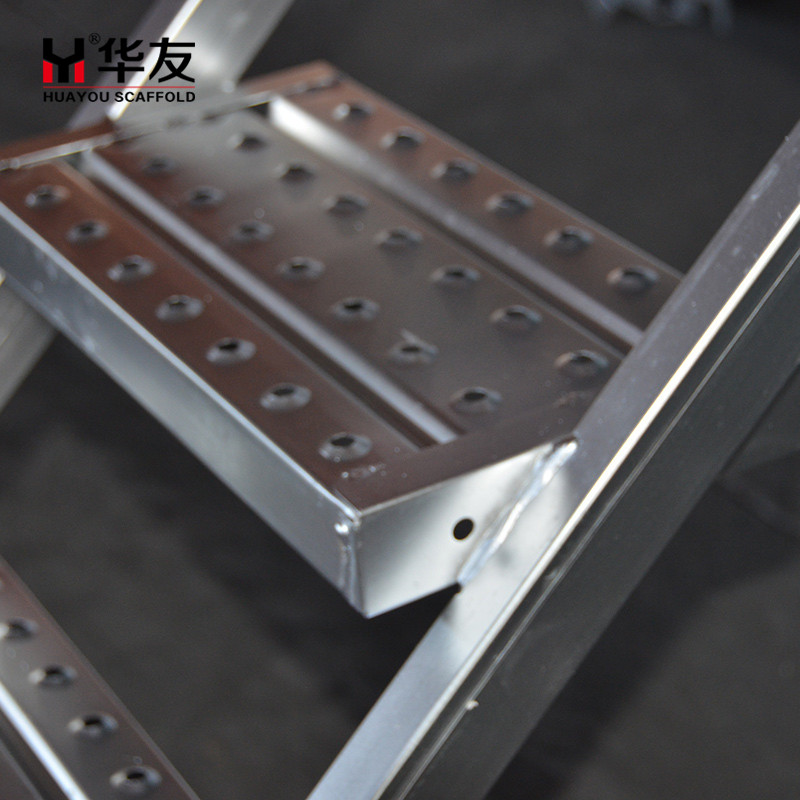
At January’s Futurebuild trade show, the sintered aluminium piece, a new design of a scaffold coupler, was being clanged and bashed against the kind of cold, metal framework it is designed to join together. For more than 100 years, the design of scaffold couplers hasn’t changed, so those clanging and bashing know just how much they should withstand, they know how long it usually takes to screw the part tight and they know when they’ve come across big potential.
“They got it immediately,” LUMA-ID Director and Product Designer Mark Little told TCT a week later. “It’s really satisfying when you spend so much time designing something and it’s used by people in the trade for the first time, slamming it against the scaffolding, doing their thing, and they [were asking] ‘when can I have this?’”
The civil engineer who thought up the coupler design is a Managing Partner of StrucTemp, a structural and temporary works service, with more than 36 years’ experience. In that time, Shiraz Dudhia has been hurdling and ducking the threaded studs that stick out of traditional couplers asking, ‘has nobody come up with anything better than this?’
Explaining that frustration to LUMA-ID has led to the design of a scaffold coupler with no external or sharp parts and a shortened thread that allows users to screw the device to a close in as little as two seconds. This design, which also has typical wall thicknesses and dimensions, has been validated over the course of 18 months using SOLIDWORKS software and fused deposition modelling (FDM) technology.
“At Luma, we’re not big fans of overly theorising. We like to print something, test it and see how well it works and where it fails,” Little said. “When you’re working with something so handheld and repetitive, you don’t want to spend hours on an idea if you haven’t tested it out first.”
With FDM, the coupler was printed in two parts and riveted together, but as the Futurebuild show approached, they looked instead to direct metal laser sintering (DMLS). With DMLS, which LUMA outsourced, the couplers were printed in aluminium in a single part and designed as a fold piece with gaps to limit the amount of redesign as they move into production.
What process will be used for the manufacture of the scaffold coupler is still to be decided – metal folding is an option the partners have prepared for, but casting remains on the table. While it won’t make much sense to additively manufacture the pieces – “the numbers of worldwide production of scaffold couplers are bonkers. I don’t want to quote them because they don’t sound real.” – the technology has still had a major role to play.
“3D printing gets you 80% of the answer and that’s enough to feel confident and go ahead on tooling. It will be slightly different properties, things might crack and fail, but you put your engineering hat on and try to avoid anything obvious,” said Little of moving into production. “I’m always a big fan of going to a supplier and saying, ‘we’ve got this; what would be the best thing to do from a cost perspective?’ Then, we can design around that.”
Want to discuss? Join the conversation on the TCT Additive Manufacturing Network .
Get your FREE print subscription to TCT Magazine.
Exhibit at the UK's definitive and most influential 3D printing and additive manufacturing event, TCT 3Sixty .
Part of Rapid News Group

Scaffold Builders © Rapid News Publications Ltd. A Rapid News Group Company. All Rights Reserved